Table of Contents
ToggleStrain gauge is a device used to measure strain of the object. Before going into details of it, let’s see something about strain.
What is Strain?
- Strain is the amount of deformation experienced by the body in the direction of force applied, divided by the initial dimensions of the body. More specifically, strain (ε) is defined as the fractional change in length.
- Strain can be of two types
- Tensile Strain: The deformation or elongation of a solid body due to applying a tensile force or stress is known as Tensile strain. In other words, tensile strain is produced when a body increases in length as applied forces try to stretch it.
- Compressive Strain: Compressive strain is the deformation in a solid due to the application of compressive stress. In other words, compressive strain is produced when a body decreases in length when equal and opposite forces try to compress it.
- Strain can be positive (tensile) or negative (compressive). Although dimensionless, strain is sometimes expressed in units such as mm/mm or inch/inch.
- In practice, the magnitude of measured strain is very small. Therefore, strain is often expressed as microstrain (μe), which is e x 10-6.
Strain Gauge
- Strain Gauge is a device used to measure deformation (strain) of an object. They have been developed for the accurate measurement of strain.
- Basically, all strain gauges are designed to convert mechanical motion into an electronic signal.
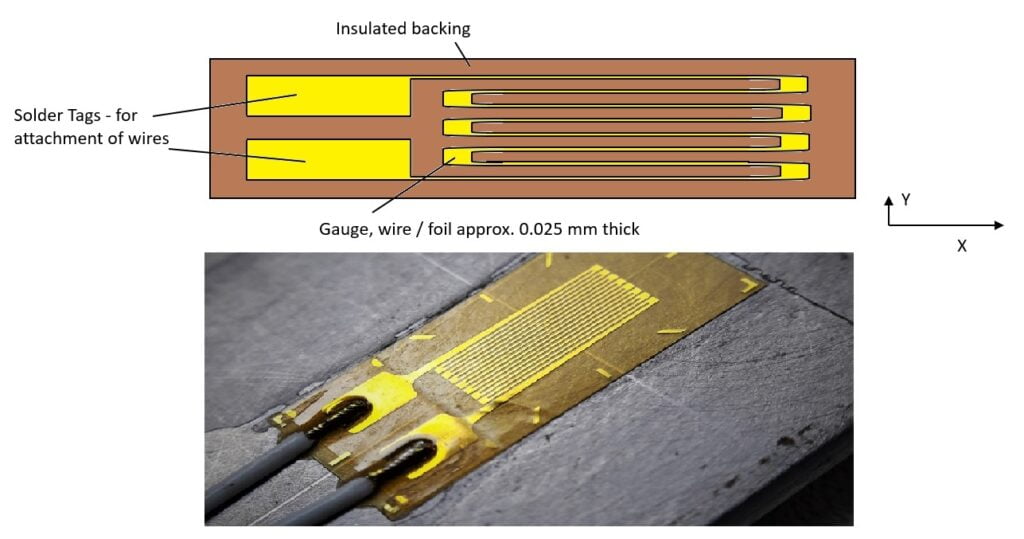
- The gauge shown here is primarily sensitive to strain in the X direction, as the majority of the wire length is parallel to the X axis.
- Strain gauge is also known as “Bonded Gauge”. The name bonded gauge is given because they are glued to a larger structure under stress (called the test specimen).
- Gauge length is an important consideration in strain gauge selection. The gauge length is the dimension of the active grid as measured inside the grid end loops. The gauge length(GGG) ranges from 0.2 mm to 100 mm.

Effect of Strain on Resistance of Strain Sensor
Following schematic shows how the strain gauge resistance varies with strain (deformation). On applying force, a change in resistance takes place.

Tension causes resistance increase and compression causes resistance decrease.

Types of Strain Gauge

Strain gauge can measure strain in one direction only. But it may be used is used to find the strain in a different direction.
In order to measure strain, forces, and deformation in multiple axes, strain gauge rosettes are used. A strain gauge rosette with two gauges can be used if the direction of principal stresses is known.
- Uniaxial: Gauge with a single grid for measuring strain in the grid direction.
- Biaxial Rosettes: Gauge with two perpendicular grids used to determine principal strains when their directions are known.
- Three-Element Rosettes: Gauge with three independent grids in three directions for ascertaining the principal strains and their directions.
- Shear Patterns: Gauge having two chevron grids used in half-bridge circuits for direct indication of shear strains (difference in normal strains).
Strain Gauge Installation
The Strain Gauge is bonded to the specimen under test, only after the following processes.
- Cleaning the surface using a degreaser.
- Cleaning it again with a conditioner solution (mild acid that accelerates the cleaning process).
- Applying a base (base neutralizes any chemical reaction introduced by the Conditioner).
- Finally, it is bonded with a super glue on the specimen.
The Bonded Metallic Strain Gauge

- The Strain Gauge has 2/4/6 leads which exhibit variation in resistance when strain is applied.
- It consists of a very fine wire or metallic foil arranged in a grid pattern. The grid pattern maximizes the amount of metallic wire or foil subject to strain in the parallel direction.
- The grid is bonded to a thin backing, called the carrier, which is attached directly to the test specimen. The strain experienced by the test specimen is transferred directly to the strain gauge, which responds with a linear change in electrical resistance.
Gauge factor (GF) or strain factor of a strain gauge is the ratio of relative change in electrical resistance R, to the mechanical strain ε.
The gauge factor is defined as:
Measuring Circuit
- In order to measure strain with a bonded resistance strain gauge, it must be connected to an electric circuit that is capable of measuring the minute changes in resistance corresponding to strain.
- Strain gauge is connected in a Wheatstone bridge circuit. A strain gauge bridge circuit indicates measured strain by the degree of imbalance. It provides an accurate measurement of that imbalance.
Wheatstone Bridge
In Figure, R1, R2, R3 are fixed resistors and Rg is Strain sensor which varies with strain. The voltage, Vin, is applied between points A and C. The variable strain sensor has resistance Rg, while the other arms are fixed value resistors. The sensor, however, can occupy one, two, or four arms of the bridge, depending on the application.
The bridge is considered balanced when R1/R2 = Rg/R3 and, therefore, Vout equals zero.
At normal condition, that is balanced bridge, Vout between points B and D will show no potential difference. (Vout =0)

Any small change in the resistance of the sensing grid will throw the bridge out of balance, making it suitable for the detection of strain. A small change in Rg will result in an output voltage from the bridge.
The total strain, or output voltage of the circuit (Vout) is equivalent to the difference between the voltage drop across R1 and R4, or Rg.
It is given by Vout = Vcd – Vcb
If the gage factor is GF, the strain measurement is related to the change in Rg as follows
Advantages of Strain Gauge
- It is very small in size and reusable.
- There is no moving part and hence no wear.
- It is very precise.
- It requires low maintenance and inexpensive
Disadvantages of Strain Gauge
- They measure strain in only one direction, a single strain gauge has its sensitivity of the strain in one direction only.
- It is sensitive to temperature. If the temperature is more, resistance will be more and vice versa.
- It is non-linear.
- It needs regular calibration.
Applications of Strain Gauge
- In load cells for weighbridges, scales, vehicles and in medical and educational applications.
- For monitoring structures such as bridges and buildings.
- Strain gauge technology is used within passenger occupancy detection systems to indicate when passenger airbags should be engaged.
- They can be bonded to the railway lines themselves to monitor and measure the stress the lines are under.
Recent posts
Related posts:
- Industrial Computerized Tomography
- Measurement of Vibration
- Electrical Telemetry | Telemetry System
- Non-Destructive Thickness Measurement
- Humidity Measurement
- Smoke and Fire Detection | Heat and Smoke Detectors
- Thermal Conductivity Measurement
- Piezoelectric Transducer
- Signal Conditioning
- Transducer and Its Classification
- Selection Criteria of Transducer
- LVDT Linear Variable Differential Transformer
- Hall Effect Transducer
- Photoelectric Transducers
- Light Sensors or Photosensors
- Resistance Temperature Detectors or Resistance thermometer
- Thermocouple
- Sensors and Transducers
- Thermistors
- X-Y Recorder or XY Plotter
- Voltage and Current Telemetry System
Hi electronicsforyou.in administrator, Your posts are always well structured and easy to follow.
To the electronicsforyou.in administrator, Your posts are always informative and well-explained.
Dear electronicsforyou.in admin, Your posts are always interesting.