Table of Contents
ToggleMeasurement of vibration is very important in industrial field. In this tutorial, vibration measurement is explained in details.
What is Vibration?
Definition: Periodic back-and-forth motion of the particles of an elastic body or medium, commonly resulting when almost any physical system is displaced from its equilibrium condition and allowed to respond to the forces that tend to restore equilibrium is known as Vibration.
Vibration means the state of an object moving repetitively back/forward, right/ left or up/down. Vibration is generally expressed by Frequency, Displacement, Velocity, and Acceleration. These four elements are generally denoted as F, D, V and A respectively.
Vibration can be divided into three types based on human perceptions; “slow motion and visible” “invisible but sensible by touching” and “insensible by touching, but audible as abnormal noise”.
Types of Vibration
Random: Such vibration lasts only for a short while, as a response to a random event. Such vibration is also known as stochastic vibration. The value of random vibration can cannot be predicted mathematically.
Such phenomena are caused by single or random excitation, and the system responds to the same in its own typical manner.
Periodic: Such vibration stays as a steady repeating phenomenon and has a specific period over which it repeats itself. It is always response to an alternating force.
Example: Machinery Vibration
Such vibration displays a periodic time function. The value of periodic vibration can be predicted mathematically by some mathematical rules, like a sine wave or the sum of many sine waves.
Thus, the concepts of frequency and the time-period are associated with periodic vibrations.
Possible Causes of Machine Vibration
- Bearing damage.
- Damaged or worn-out gears.
- Loose bearings, loose bolts and corrosion can result in excessive machine vibration.
- When two or more rotating machines are connected, the correct alignment is very important. Misalignment may result in vibration.
- When the centre of gravity of a rotating object is not exactly in the centre line, it causes machine unbalance resulting in vibration.
- Every machine has one or more resonance frequencies (natural frequency). When a rotation frequency coincides with the resonance frequency of the machine, resonance occurs.
Effect of Vibration
- If unchecked, above causes create large and destructive periodic forces, which lead to metal fatigue, and eventual failure of the machinery.
- Equipment that is showing excessive vibrations will most likely not achieve the expected lifespan, and can stop working anytime or can cause dangerous situations.
- When a machine is unbalanced, it can cause damage to the machine itself, the foundation, pipes, etc.
- Due to the mechanical forces in the machine, loose parts can rapidly cause damage.
- Vibration of machine requires kinetic energy which is loss of energy.
- Vibration causes operator fatigue, noise and other irritation.
Taking accurate vibration measurements before machinery breaks down. Similarly, infrastructure is brought to a halt and disaster occurs is vital in order to prevent secondary accidents. Therefore, it is important to find the root cause of vibrations by measuring and analysing the vibration signals.
Why Measurement of Vibration is Necessary?
- Excessive vibration can cause machine damage which may results in huge cost and time to repair. Vibration measurement and necessary actions save machine from damage.
- Proper functioning of machine can prevent accidents, extra noise and operator fatigue. This results in increase in productivity and profit.
How to Measure Vibration?
As stated earlier, Vibration is generally expressed by Frequency, Displacement, Velocity, and Acceleration.
Frequency Analysis (F)
Frequency means the number of times a vibrating object generates a repetitive motion in a second. Its unit is hertz (Hz).
Frequency analysis is the technique which is used for identifying the frequencies of the various components of the vibration, and their associated magnitudes. Each frequency corresponds to a specific mechanical cause.
Displacement (D)
Displacement means peak to peak distance of vibration of a vibrating object.
All vibration is the to and fro movement of a body. In terms of vibration, Displacement is low frequency vibration. In displacement measurement, movement of body from one end to another is measured. Unit of displacements is μm or mm.
Velocity (V)
Velocity means the rate of change of displacement with respect to time.
The first differential displacement dD/dt gives the rate of change of displacement, which is velocity. This is the most commonly measured parameter.
Velocity places even emphasis on low and high frequencies of vibration. Unit of velocity is mm/sec or cm/sec and this is normally true RMS.
It is most common mode of measurement of vibration.
Acceleration (A)
Acceleration means the rate of change of velocity with respect to time.
The second differential displacement d2D/dt2 is computed gives acceleration. Which is nothing but the rate of change of velocity. Acceleration emphasizes high frequencies. Unit of acceleration is m/sec2.
Vibration Transducer Types
Considering principle of working there are vibration displacement, velocity and acceleration transducers. They are used as per the suitability in industrial application.
The relationship between the frequencies associated to the mechanical defect and the rotating frequency of the shaft used as a reference provides precise information to determine the nature of it due to the vibration. Therefore, Vibration transducers must also be very accurate regarding the frequency information contained in the mechanical signal.
The different types of transducers respond to different frequency of vibration is shown in the following table
Type of Transducer | Operating Frequency Range |
Displacement Transducer or proximity probe | Low |
Seismic velocity transducer | Low and high |
Piezoelectric transducer or accelerometer | High |
Displacement Transducer
Construction and Working of Displacement Transducer
The displacement transducer, is generally used for low frequency measurements (below 1,000 Hz). It is a proximity probe. Proximity transducer works on the principle of “Eddy current” hence also known as Eddy current probe.
The displacement transducer is as shown in the following figure.
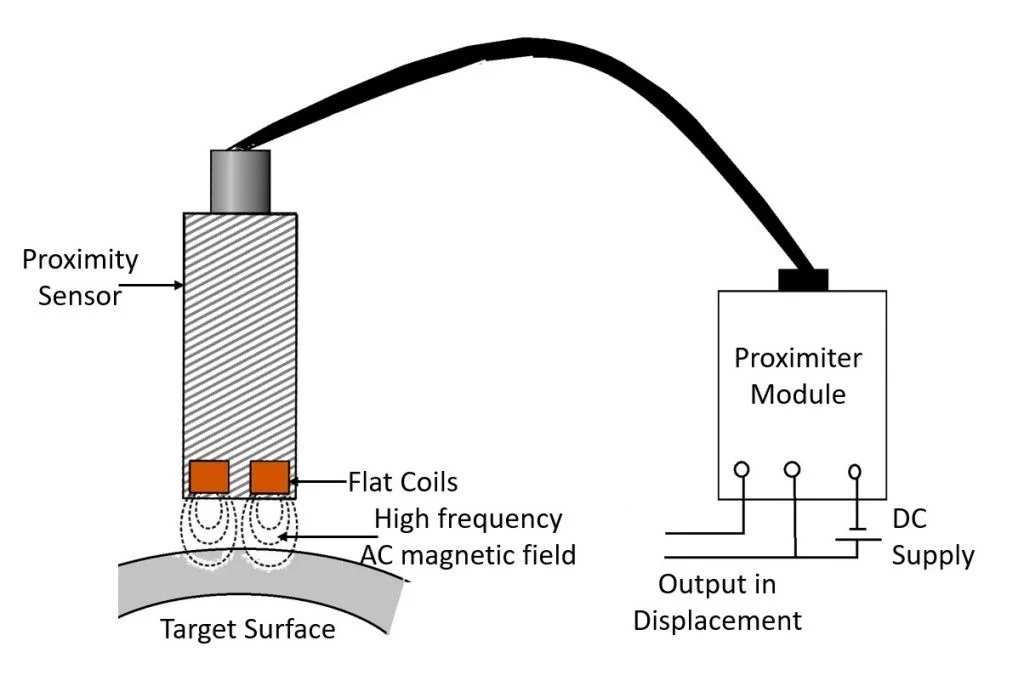
They are installed in or on the bearing caps and detect the displacement of the shaft in relation to its rest position. It sets up a high-frequency electric field in the gap between the end of the probe and the metal surface that is moving.
It has frequency response is excellent. They do not have a working frequency lower limit. It means that, the minimum frequency is zero. It can also measure static displacement. They are used in the measurement of shaft vibration, shaft axial position and casing expansion.
Advantages of the Displacement Transducer
- It measures the relative movement between the sensor tip and the rotating shaft.
- It measures very slow relative movement like thermal expansion.
- It is particularly useful in rigid machinery where very little vibration is transmitted from the shaft to the machine casing.
Disadvantages of the Displacement Transducer
- Displacement transducers are sensitive to shaft surface defects such as scratches, dents and vibrations in conductivity and permeability.
- The frequency range is limited to between 0 Hz to 1000 Hz.
- A signal conditioner is required.
- Measures relative displacement not absolute displacement.
Velocity Transducer
Construction and Working of Velocity Transducer
The velocity seismic transducer consists of a permanent magnet located in the center of a copper wire coil. When the housing vibrates, a relative movement is created between the magnet and the winding.
According to Faraday’s law of electromagnetic induction, the relative motion between the permanent magnet and the coil generates a voltage that is proportional to the velocity of the motion.
The seismic velocity transducer is shown in the following figure.

Advantages of the Velocity Transducer
- It is an active transducer so external power supply is not required.
- Generated voltage is directly proportional to the vibration therefore velocity can be directly measured.
- Allows you to send the electrical signal over long distances by cable, making it ideal for remote operations.
- It has a very good signal to noise ratio (SNR) within its frequency range.
Disadvantages of the Velocity Transducer
- The velocity transducer is relatively large. This mass of velocity transducer can significantly affect the vibration output on small devices
- The transducer output varies with temperature. At high temperatures, the output can reduce due to the weakening of the magnetic field.
- The coil in the velocity pickup is sensitive to external electromagnetic fields.
- During measurement, vertical or horizontal orientation of the transducer can change the output around 5-10%.
Acceleration Transducer
Construction and Working of Acceleration Transducer
The most common acceleration transducer is the piezoelectric accelerometer. It consists of quartz crystal. This type of transducer generates an electric voltage that is proportional to acceleration, due to the pressure applied on a piezoelectric crystal.
The acceleration transducer (accelerometer) is shown in the following diagram.

These transducers are well suited for taking high-frequency vibration data, where large forces with relatively small displacements have to be detected. Some special transducers can measure much lower frequencies from 5 Hz and also much higher frequencies upto 25KHz. The frequency range depends upon size of transducer
Advantages of the Acceleration Transducer
- These transducers are very compact, light and small, no moving part.
- They need small magnetic bases for temporary mounting.
- Can be easily mounted with adhesive or screwed.
- Most sensors have a wide frequency range, usually between 5 Hz and 25,000 Hz.
Disadvantages of the Acceleration Transducer
- The amplitude output can be given in acceleration. This output must be integrated to obtain the velocity value.
- The amplification that occurs at or near resonance is significant and must be avoided, or at least identified.
Piezoelectric Velometer
It is a device which is used to measure velocity of vibration. A piezoelectric velometer has same construction as an accelerometer, but with a signal amplifier that performs an integration of the signal. The device which performs integration consist of an integrator circuit.
The signal output is given directly in velocity units because integration is done inside the velometer.
The velometer has good frequency response characteristics of an accelerometer, therefore it generates a linear output over a much larger frequency range than the seismic velocity transducer.
For MCQ on Vibration Measurement
Recent posts
Related posts:
- Industrial Computerized Tomography
- Electrical Telemetry | Telemetry System
- Non-Destructive Thickness Measurement
- Humidity Measurement
- Smoke and Fire Detection | Heat and Smoke Detectors
- Thermal Conductivity Measurement
- Piezoelectric Transducer
- Signal Conditioning
- Transducer and Its Classification
- Selection Criteria of Transducer
- Strain Gauge
- LVDT Linear Variable Differential Transformer
- Hall Effect Transducer
- Photoelectric Transducers
- Light Sensors or Photosensors
- Resistance Temperature Detectors or Resistance thermometer
- Thermocouple
- Sensors and Transducers
- Thermistors
- X-Y Recorder or XY Plotter
- Voltage and Current Telemetry System
To the electronicsforyou.in administrator, Thanks for the informative and well-written post!
To the electronicsforyou.in owner, Thanks for the comprehensive post!